关注作者了解更多
我的其他CSDN专栏
关注作者了解更多
资料来源于网络,如有侵权请联系编者
目录
回顾:集成电路制造流程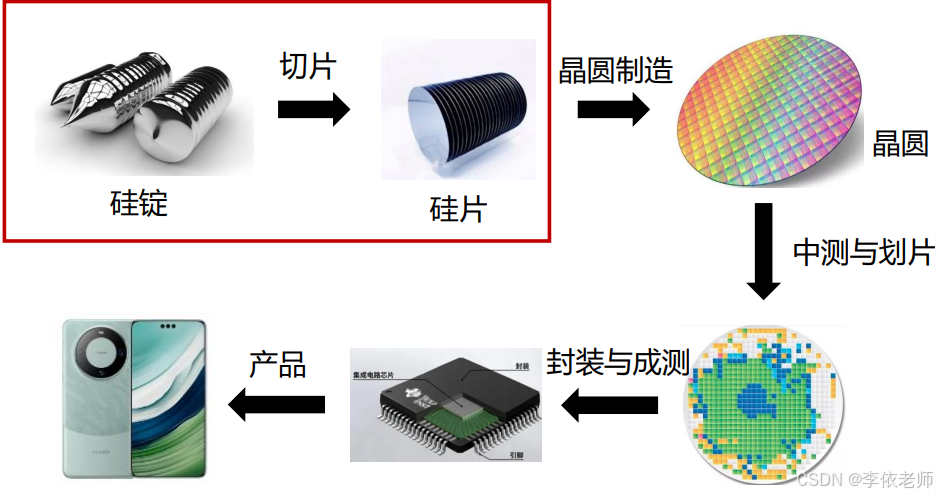
为什么用硅晶体制造集成电路?
原料充分:沙子(石英砂或硅石,主要含SiO2)是硅在自然界中存在的主要 形式,自然界大量存在且易于获得。
氧化层保护:暴露在空气中,表面会生长出几个原子层的本征氧化层;在高 温氧化下,会进一步生长一定厚度性能稳定的氧化层。氧化层对硅晶片表面 的元器件结构起到了很好的保护作用。
密度小:硅单晶密度为2.33g/cm3,只有锗或砷化镓密度的43.8%。
热学性质好:热导率高,且膨胀系数小。
工艺性能好:拉制的单晶锭缺陷密度低、直径大,能够制造出晶格完整的大 尺寸硅片。目前可达18英寸(450mm)。
力学性能好:可以采用硅微机械加工技术制作微小结构元件。
硅晶胞
晶体中能反映原子周期性排列基本特点及三维空间格子对称性的基本单元 称为晶胞。
在立方单元8个顶点上各有1个原子,立方单元的6个面的面心处各有1个原 子,立方单元中心到顶角引8条对角线,在其中不相连的4条对角线的中点各 有1个原子。晶胞的边长是晶格常数a(硅晶体的晶格常数a=5.4305A)。
硅晶体中还有较大的“空隙”(约为66%)。正因如此,杂质原子能较容易 地进入硅晶体中
硅单晶的晶向与晶面
任何晶列的取向可以由连接晶列中相邻格点的矢 量 的方向来标记。 称为晶向指数
对于晶面的标记,可以用相邻的两个平行晶面在x,y,z轴上的截距来表示 称它们为晶面指数,又称密勒指数
集成电路工艺是基于不同产品特性采用不同晶面
硅片的制备流程
多晶硅制备(冶炼)
冶炼是采用木炭或其他含碳物质如煤、焦油等来还原石英砂,得到硅。硅的含量在 98%~99%之间, 称为冶金级硅。
冶金级硅也称为粗硅或硅铁。粗硅中主要含有铁、铝、碳、硼、磷、铜等杂质。这种纯度的硅是冶 金工业用硅,微电子工业用硅只占其中的5%不到
多晶硅制备(提纯)
蒸馏法提纯
经过提纯后的多晶硅纯度可达99.999999999%
单晶硅制备(直拉法)
1918年,柴可拉斯基(J.Czochralski)从熔融金属中拉制出了金属细灯丝,因此直拉法又称柴式法。
硅的熔点为1417℃,坩埚内熔体温度一般控制在1417~1420℃之间。 熔体上部与晶体接触位置的熔体温度低于熔点。因此,提拉硅锭时熔 体/晶体界面的熔体就自发地转变为和硅锭相同晶向的晶体。
晶体参杂
集成电路工艺使用的衬底硅片既有本征型的,又有掺杂型的,根据不同微电子产品工艺特点,选用特定导电 类型和电阻率的硅片作为衬底材料。因此,在单品生长时,需要在硅锭中掺入一定量的特定III、V族杂质
液相掺杂是在单晶生长过程中最常用的掺杂方法,有两种掺杂方式:直接掺杂和母合金掺杂。
直接掺杂是指将所需杂质单质按剂量直接加入到坩埚的多品硅中,这种方法适用于制备重掺杂的硅锭。
母合金掺杂是指将杂质元素先制成硅的合金,如磷硅合金、硼硅合金,然后,再按照所需的剂量将合金加 入到坩埚的多晶硅中,这种方法适用于制备轻掺杂和中等浓度掺杂硅锭。
气相掺杂是指在单晶炉内通入的惰性气体中加入一定剂量的含掺杂元素的气体,在杂质气氛下,蒸 发常数小的杂质部分溶入熔体硅中,再被掺入单品体内,或直接由气相扩散溶入晶体硅中的掺杂方 法。例如,在单晶炉内惰性气氛中掺入稀释的磷烷(PH3)[或乙硼烷(B2H6)拉制n型(或p型)单晶硅 锭。气相掺杂方法难以制备轻掺杂的高阻硅。
切制硅片
切断→滚磨→定晶向→切片→倒角→研磨→腐蚀→抛光→清洗→检验
切除单晶硅锭的头部、尾部及超规格部分,将单晶硅锭分段成切片设备可以处理的 长度,应切取试片测量单晶硅锭的电阻率和含氧量等。
滚磨
通过外径滚磨获得较为精确的直径
定晶相
切片
倒角
研磨
腐蚀
在经切片及研磨等机械加工之后晶片表面受加工应力而形成的损伤层使用腐蚀方 法去除工艺。腐蚀方式有酸性腐蚀和碱性腐蚀,酸性腐蚀是最普遍方法
抛光
清洗
检验
检测晶片表面清洁度和平整度等情况。检验合格的硅片就可以装箱售出
硅片的规格
按硅片直径划分
按参杂类型等参量划分
外延
外延一词来自希腊文Epitaxy,是指“在……上排列”。在集成电路制造工艺中,外 延是指在晶体衬底上,用化学或物理方法,规则地再排列所需的半导体晶体材料。新 排列的晶体称为外延层,有外延层的硅片称为外延硅片。外延工艺要求衬底必须是晶 体,而新排列得到的外延层是沿着衬底晶向生长的,因此与衬底成键晶向也一致。
气相外延
气相外延(Vapor Phase Epitaxy, VPE)是指含外延层材料的物质以气相形式流向 衬底,在衬底上发生化学反应,生长出与衬底晶向相同的外延层的外延工艺。